answers for procedures for normal operations of the gas filling station facility
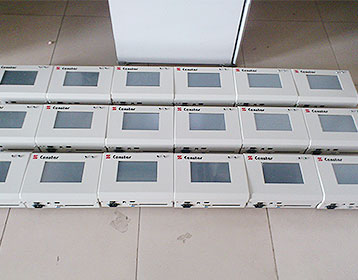
Propane Bottle and LP Gas Cylinder Filling
Cylinders that propane dealers most often fill are the 20 pound bottles commonly used for gas grills. Because there are different types and sizes of cylinders, the filling process is not always the same as requirements vary by cylinder. This section will hopefully answer questions people may have when taking their bottle to be filled.
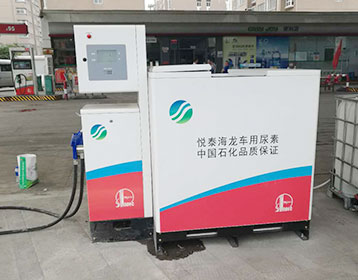
Comprehensive Facility Operation & Maintenance Manual
O&M Manuals provide procedures to operate and maintain a facility's various systems and equipment. It is important to analyze and evaluate a facility from the system level, then develop procedures to attain the most efficient systems integration, based on as built information and the
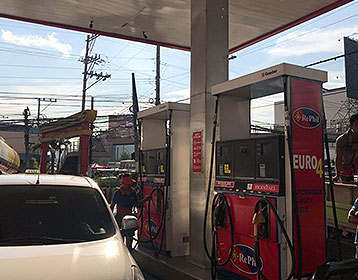
Lesson 8: Landfill Equipment and Operating Procedures
Lesson 8: Landfill Equipment and Operating Procedures. A run on control system should prevent liquid from flowing onto the active portion of the landfill during the peak discharge from a 25 year storm event. The run on system also should collect and redirect surface waters entering the landfill boundaries.

o CHAPTER VIII 5 02
Revised May, 2002 VIII 3 All operators must follow these basic rules: • Ensure that all natural gas in distribution mains and service lines is odorized. • Specify or determine the type of odorant used in the system. • Specify in the operations and maintenance plan the manufacturer's recommended amount of odorant per million cubic feet (mmcf) of gas.
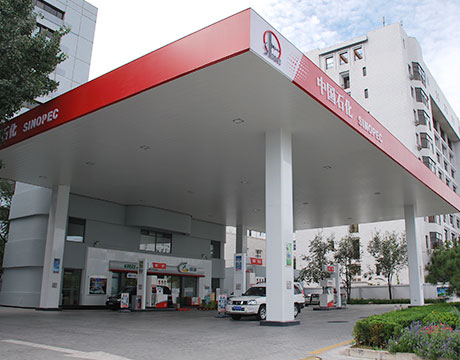
PLANT START UP AND SHUT DOWN SEQUENCE
2 Gas Storage System Gas pressure in normal pressure Local Gauge Before filling, it is required to assure whether all manual drain valves for emptying of system lines are closed and all instrumentation root valves are manipulated for filling. Vent valves are closed manually after confirmation of
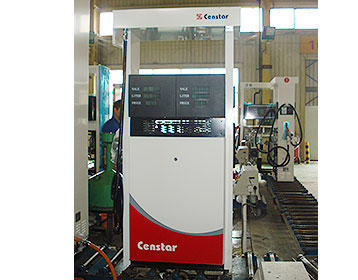
Petroleum Gas Station Checklist Retail Blog
Note: A user should be able to read the signs without strain. A minimum value of 50 lux is required for LP Gas filling and is recommended for flammable liquid filling) Minimum of two powder type fire extinguishers provided at service station; Minimum rating
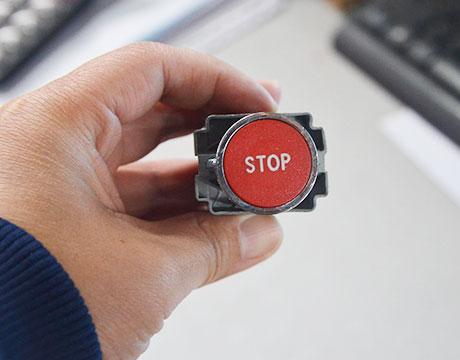
LP Gas Basic Filling Procedures General Information
LP Gas Basic Filling Procedures General Information Warning: Dispensing station to be operated only by a person who is certified according to Utah State Fire Prevention and Safety Law Title 53 Chapter 7 Part 3 Liquefied Petroleum Gas Act. The State Fire Marshals Office is not to be considered a source of training in the dispensing of propane.
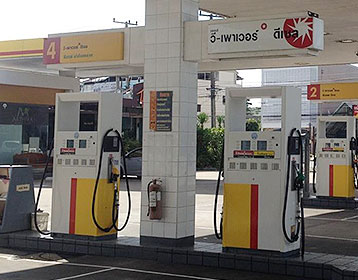
37 Best Standard Operating Procedure (SOP) Templates
37 Best Standard Operating Procedure (SOP) Templates For organizations or institutions which desire that certain activities are done by following a strict set of steps, the standard operating procedures, SOPs could come in handy for them.
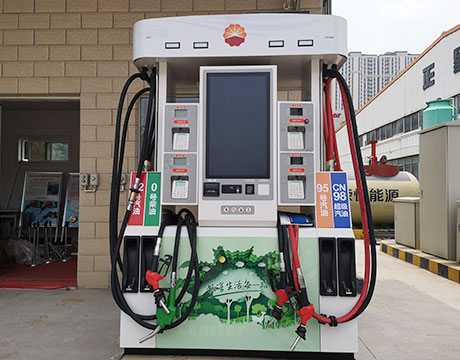
Work Health and Safety Act 2011 WorkSafe Queensland
PN11388 Version 3 Last updated June 2018 A guide for service station operators under the Work Health and Safety Act 2011 Page 4 of 19 1. Introduction The Work Health and Safety Act 2011 (the WHS Act) regulates the safe management of hazardous chemicals including flammable and combustible substances at Queensland workplaces.
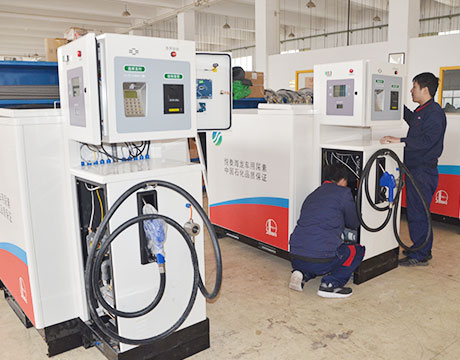
Standard Procedures for Tank Cleaning, Purging and Gas
Standard Procedures for Tank Cleaning, Purging and Gas free Operation for Oil tankers Tank cleaning The process of removing hydrocarbon vapours, liquids or residues. Tank cleaning may be required for one or more of the following reasons: To carry clean ballast. To gas free tanks for internal inspections, repairs or prior to entering dry dock.
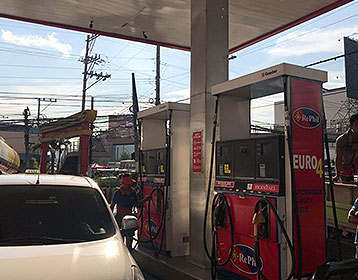
05.0 Operating Procedures Petsec Energy Ltd
The production operations personnel on the facility perform these and other day to day tasks: 2.2.1 Monitor safe operating limits of production components: pressures, temperatures, flow rates and liquid levels. 2.2.2 Adjust pressures, temperatures, flow rates and/or liquid levels as the operating limits change.
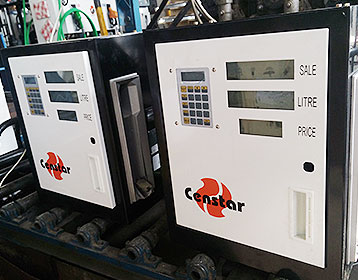
Pipeline Pigging and Its Operation PIPING GUIDE
Pipeline Pigging and Its Operation Posted by Akki on and fully monitored by all pipeline users but the actual procedures laid down for each pig launching/pig receiving facility will vary. vessel on the facility, in hydrocarbon service, which is regularly opened to the atmosphere and then pressured as a normal operating procedure.
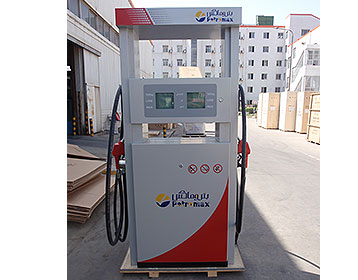
Propane and Liquified Petroleum Gas Regulations
The order to discontinue operation will require the owner or operator to discontinue the use of the container or LPG facility within 24 hours. After the container or LPG facility is sealed, it may not be returned to service until the violations have been corrected, the repairs have been made and the Department removes the seal.
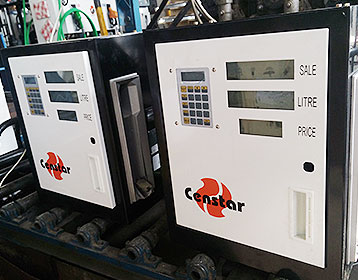
Safety and Health Information Bulletins Potential Carbon
Carbon dioxide is a colorless, odorless gas and should be treated as a material with poor warning properties. It is denser than air and high concentrations can persist in open pits and other areas below grade. The current OSHA standard is 5000 ppm as an 8 hour time weighted average (TWA) concentration. Gaseous carbon dioxide is an asphyxiant.
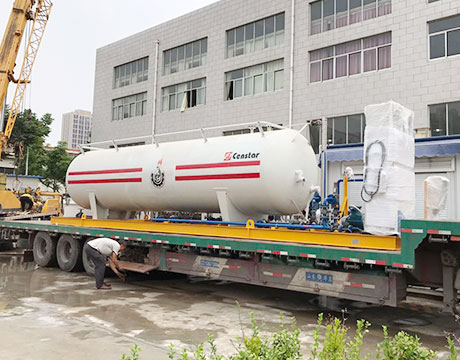
Facilities and Equipment: CGMP Requirements
A cleanroom (facility) that is complete and ready for operation, with all services connected and functional, but without equipment or operating personnel in the facility •
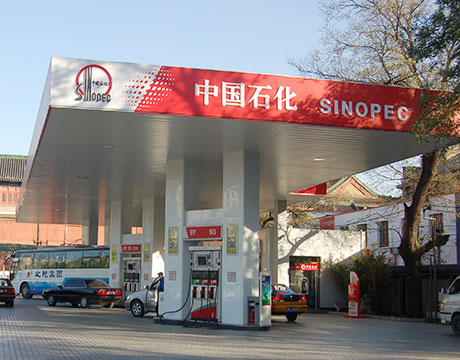
Petrol Stations Health and Safety Authority
Publications. Display clear information/warning signs setting out the traffic control arrangements. Provide sufficient designated parking areas close to the shop and away from the pumps. Provide mechanical protection to vulnerable structures such as fuel tanks and liquified petroleum gas
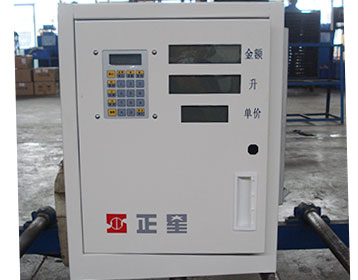
101 Recognizing and Reacting to Abnormal Operating
Abnormal Operating Conditions 101 Recognizing & Reacting to AOC’s Performance Checklist [Revision 0] [Revision Date 05/28/01] component or deviation from normal operations that may indicate a condition escaping gas or liquids at a regulator station or other above ground facility including (as relevant): • Detection
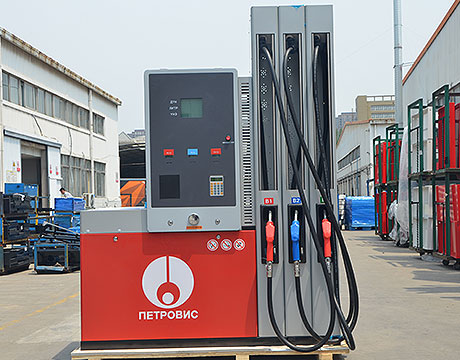
Facilities and Equipment: CGMP Requirements
A cleanroom (facility) in normal operation, with all services functioning and with Written sanitation procedures to include schedules, methods, equipment materials for
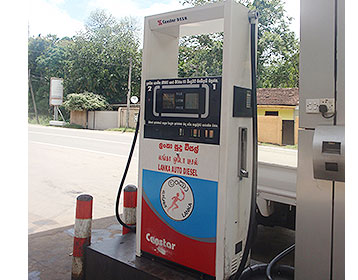
AOC Flashcards Quizlet
Operations and/ or other appropriate personnel should determine the exact cause and take decisive action to control the condition, while adhering to company policy and procedures. Suppose a pipeline system with multiple stations is flowing with all units running.
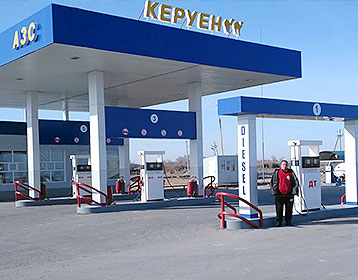
FILTRATION Environmental Protection Agency
9 operating procedures associated with normal process conditions 37 9.1 indicators of normal operating conditions 37 9.2 process actions 37 9.3 process calculations 40 9.3.1 filtration rate 40 9.4 recordkeeping and quality control 40 9.5 filter monitoring instrumentation 41 10 operating procedures associated with abnormal process conditions 43